Anti-lock braking systems (ABS) reduce accidents and help save lives. This is well known and proven for two- or four-wheel vehicles. Although two-wheeled motorcycles and scooters are not yet widely used in ABS systems like four-wheeled vehicles, there are more and more reasons to support their widespread adoption of ABS systems in the future.
This article refers to the address: http://
Freescale Semiconductor is a leading semiconductor supplier to the ABS system, which was the case when the technology was widely used in ground vehicles in the 1980s. Freescale has a long history and insights into applications that strategically understand and address industry requirements for unicycle, tandem and scooter applications.
Benefits of the ABS system for motorcycles and scooters
The ABS system was first used in high-end cars in 1978. Since 2007, all new factory cars sold in the EU have to be equipped with ABS systems [1]. In the United States, the National Highway Traffic Safety Administration issued the US Federal Motor Vehicle Safety Standard (FMVSS 126) on September 1, 2011, requiring passenger cars with gross weights of 4,536 kilograms (10,000 ($0.1020) pounds) or less. Multi-purpose vehicles, trucks and buses must use an electronic stability control system (ESC, built-in ABS) [2]. In India, the government began in 2015 to require new passenger cars and other four-wheeled vehicles to install the ABS system [3].
In 2013, the global motorcycle sales volume was 99.5 million, the motorcycle industry is expected to achieve an annual growth of 5.9%, and sales in 2018 will reach 132.4 million [4]. Similar to the history of cars using the ABS system, the first two-wheel ABS brake system was installed on high-end motorcycles in 1988. Although several manufacturers now offer ABS systems, these systems are mainly used for high-end models and have not been extended to small-displacement locomotives. In India and China, the largest sales are dual-engine cars, motorcycles and scooters with a displacement of less than 150 cc, accounting for 90% of market sales [5]. Figure 1 shows that sales of dual-engine vehicles in China and India are growing. In 2014, the global ABS penetration rate is expected to be close to 4%, while the current ABS penetration rate in India and China is 0% [5].
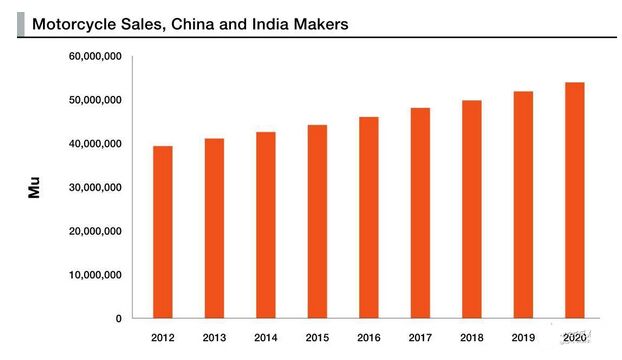
Figure 1. Trends in dual-engined vehicles in China and India – by producers [6].
Facts speak louder than words, the following facts show the effectiveness of installing ABS systems in dual-engine cars:
• In 2006, in the EU-25, motorcycle mileage accounted for 2% of total mileage, but motorcycle accident deaths accounted for 16% of total road traffic deaths.
• According to 2013 road accident statistics, 26.3% of road traffic accidents worldwide are related to dual-engine vehicles, and the number of such accidents has reached 39,353 [3].
• According to the 2013 American Highway Safety Insurance Association (IIHS), the number of motorcycle-related deaths due to ABS is 31% lower than that of the same type of motorcycle without ABS [8].
Improve safety of motorcycles with ABS (anti-lock braking system)
• US Highway Loss Data Institute 2013 statistics show that motorcycles with ABS have a 20% lower collision risk claim rate than ABS-free motorcycles - if ABS combination controls are installed (front and rear wheels) All installed ABS) is 31% lower [8].
• For general drivers with a speed of 100 km/h, ABS can reduce the braking distance by 15% [9].
• With ABS, experienced motorcyclists and novice drivers can reduce the braking distance [8].
Figure 2 compares the effects of installed and unmounted ABS systems on motorcycles.
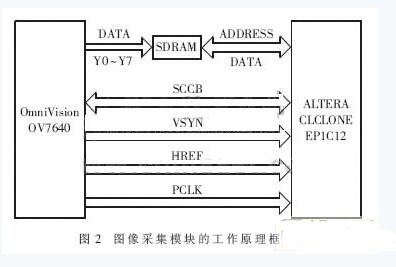
Figure 2. After installing ABS, the braking distance of the motorcycle (generally, the driver's initial speed is 100 km / h) is usually greatly reduced. After installing the ABS system, the braking distance is shortened, and the possibility of a fatal collision of the motorcycle driver is reduced by 31% [9].
Consumer reports refer to ABS as “the most valuable feature of motorcycles†[10].
Legislation to promote implementation
Even though the above discussion of safety factors is not enough to convince dual-engine manufacturers to install ABS systems, governments around the world have been convinced and asked to install them.
In 2016, the European Union will mandate that new motorcycles with engine displacements exceeding 125 cc (cubic centimeters) must be fitted with ABS [8]. By 2019, all double-engined vehicles with a displacement of more than 50 cc in the EU must be equipped with ABS. The EU directive is expected to be adopted in Asia and the Americas.
Existing and future legislation will encourage more suppliers to develop ABS braking systems for dual-engine vehicles.
ABS brake system for dual-engine vehicles
In the ABS brake system, the locomotive driving speed is measured by a wheel speed sensor or a sound wheel. The microcontroller (MCU) in the ABS Electronic Control Unit (ECU) uses these measurements to determine if the vehicle will stop. When this happens, the MCU sends an analog mixed signal (AMS) to the integrated circuit (IC) in the ECU, drives the hydraulic valve and adjusts the pressure on the pedal from the brake cylinder. This braking can occur several times per second. Figure 3 shows the position of these brake units on the motorcycle.
Improve safety of motorcycles with ABS (anti-lock braking system)
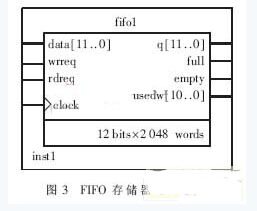
Figure 3. The motorcycle ABS assembly is similar to the ABS assembly on a four-wheeled vehicle system [7].
Typically, the first-tier suppliers of motorcycle manufacturers offer two-wheel and one-wheel systems. With the two-wheel system, the ABS AMS IC designed for passenger cars can also be used because it has enough functionality. However, to ensure the cost-effectiveness of a single-wheel system, a completely different approach must be used to achieve a single-wheel brake – a stand-alone design. This requires two completely different design/development paths. Figure 4 shows the combined output and unused outputs of the ABS AMS IC in a two-wheel system, along with the associated disadvantages, and shows a stand-alone single-wheel system solution.
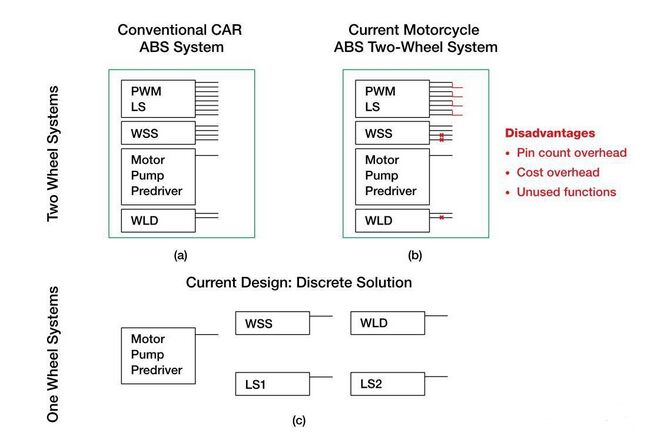
Figure 4. (a) Four-wheel ABS IC used in the current (b) two-wheel ABS design and (c) sub-legislation adopted by the single-wheel ABS. Common modules in various designs include: Pulse Width Modulation (PWM) low-side (LS) drivers, wheel speed sensors (WSS), warning light (WLD) drivers, and motor pump pre-drive modules.
The ABS technology currently used in two-wheel ABS and single-wheel ABS braking systems is not optimized and requires additional design to achieve its application in both systems. In the past, the semiconductor industry has had a major impact on how to deal with these situations. Freescale expects that if there is a fully integrated solution, it will increase the competitiveness of suppliers and improve the industry's response to the government's ABS legislation on dual-engine installations.
Improve safety of motorcycles with ABS (anti-lock braking system)
Conclusion: Safer dual-engine car
In two-wheeled vehicles, anti-lock braking systems have proven their value for accident prevention and reduction of casualties. In addition to increasing consumer demand, legislation can also drive the wider application of this technology to dual-engine vehicles around the world. Since the technology was used in ground vehicles in the 1980s, as a leading supplier of ABS semiconductors, Freescale is poised to continue to maintain its leading position, launching for two-wheel and one-wheeled motorcycles. High integrated circuits for scooter applications.
The fiberglass cloth winding tube made of alkalifree glass fabric and binded with epoxy resin, in heatrolling and tightening, baking and curing, with high mechanical property and stable electrical property in high humidity, suitable for being used as insulation structural parts of mechanical, electrical and electronic equipment.
The epoxy glass fiber sleeve is made of alkali-free glass fiber impregnated with epoxy resin solution and is wound around the axis at an angle of 50 to 60 degrees. It is formed by uninterrupted fiber wet winding and heated and cured after molding Insulation products. The product has high temperature resistance. Good insulation performance, high electrical performance and mechanical strength are easy to be processed, and can be made into B-class, F-class, H-class heat-resistant insulating products according to user requirements.
Product diameter Φ5mm-Φ5000mm, product length> 20mm or more optional, product wall thickness> 2mm or more optional, product shape cylindrical tube, square tube, hexagonal tube, special-shaped tube, oval tube.
Fiberglass Tube,Fiberglass Winding Tube,Pultrusion Fiberglass Tube,Reinforced Pultrusion Fiberglass Tube
Yingkou Dongyuan Electrical Insulation Board Co.,Ltd , https://www.dy-insulation.com