Problems encountered in flexible manufacturing
When we look at a product production line, we find that even with advanced integrated production lines, it cannot meet individualized production requirements. The traditional mechanical manufacturing is a unit followed by a unit. The conveying system sends the processed object to the processing unit for processing, such as stamping, cutting, assembling, folding, bonding, welding, etc. The conveying system will pass through the entire process. The processed product consists of one unit to another, so this will result in many constraints:
For the factory, technology and concept are not the focus of their attention. End User usually only cares about:
--How to get a high OEE in the production line
--Few failures, stable operation, even if there is a failure, but easy to maintain;
However, for flexible manufacturing, product individuation will result in difficulties in quality iteration, and the ability to change delivery will reduce the delivery capacity. Frequent replacements will cause defective products at startup/shutdown, but will not result in small batch production. The rise in yields.
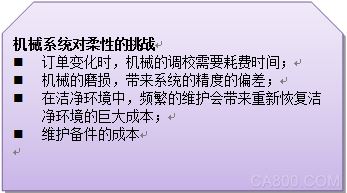
How does SuperTrak solve the problem of flexibility?
In fact, the solution to this problem lies in changing the thinking: Traditionally, the processing station is unchanged, and the product is transported along the conveying system. This is undoubtedly correct for large-volume product and fixed production, but for product specification changes, For the production of personalized products with changing production processes, you will encounter the problem of flexibility, that is, how does the machinery adapt to changes?
Yes, SuperTrak is designed according to this idea, so that the processed products and workstations can be moved to adapt to this change.
SuperTrak is a flexible electric drive transmission system developed based on long stator linear motor technology (LLM), which changes the size between the objects to be machined by the moving elements operating on the stator and the equipment such as the robot laser of the processing unit. The cutting head and the stamping station are synchronized so that the product's size, specification, and processing technology can be flexibly changed to match the processing equipment, without complicated mechanical adjustment.
Its purpose is to:
(1) When the product specification is changed, the adjustment of the machining position and spacing need not be mechanically adjusted, but can be realized only by changing the electrical parameters, especially for the production in which the batch size is small and the size and size change is relatively large.
(2) The whole line speed can have a high flexibility, which varies depending on the production load.
(3) Higher integration: The floor space of the production line will be smaller. Due to the extremely high electromagnetic response speed, there is no need to consider the accumulation of space for the product, and the acceleration/deceleration time is the same as the response speed through the traditional frequency conversion motor. It is very high, so there is no need to set a larger acceleration and deceleration space like a conventional transmission system.
(4) Improve production line OEE. For the production system, the decline of OEE includes maintenance, adjustment of the parameters when order is replaced, and the traditional transportation system, especially high-precision product manufacturing in the field of electronic semiconductors, etc., the accuracy of its fixtures is high, therefore, the adjustment will be Time-consuming, quality of finished products during the adjustment process, machine maintenance, etc. will affect the entire line of OEE.
Figure 1 - SuperTrak Linear Transmission System - High-speed cornering like F1
SuperTank can achieve a positioning accuracy of up to 10 μm, and provides a line speed of 4 m/s, while the POWERLINK real-time network can provide high-precision synchronization and positioning control.
Significant advantage
Due to the non-contact approach, this gives SuperTrak a great advantage:
(1) High-speed response: Minimal inertia of the mover to achieve fast response;
(2) No deceleration mechanism: There is no problem of transmission accuracy caused by the backlash of the traditional mechanical deceleration mechanism;
(3) No on-the-spot components of the cable drag chain;
(3) Low wear and easy maintenance - For food and pharmaceutical applications such as this one is critical because every maintenance work into the clean area brings new costs to a clean environment.
Simulation Modeling
The core of digital manufacturing is CPS- virtualizing production through simulation, including parameter optimization and production response of the control process. Since personalized production will inevitably not have enough quality iteration time and quantity, it is necessary to be able to perform parameters of the production process in advance. Optimized, SuperTrak can be integrated through B&R's Automation Studio with MATLAB/Simulink, MapleSIM, and other software. Simulation results can be directly operated on B&R controllers.
SuperTrak's simulation modeling can integrate delivery systems, robots, and movers, and integrate the response parameters, adjustments, and safety of the production process, including the suppression of fluid fluctuations in motion.
Application scenario
The application scenarios that SuperTrak adapts to include:
(1) Products with smaller production volumes have larger changes in size, such as vaccine production, pharmaceuticals and foods;
(2) The need for a clean environment to meet the pharmaceutical-grade clean requirements (made of stainless steel);
(3) Production line layout requires compact size production such as electronics and semiconductor production.
SuperTrak currently supports 10kg load and 50-meter-long line integration.
About Beccale
B&R is an innovative and driven automation company headquartered in Austria with global branches. In July 2017, B&R became a business unit of the ABB Group. As a global leader in industrial automation, B&R integrates cutting-edge technologies and advanced engineering capabilities to provide a complete solution for machine and factory automation, motion control, HMI, and integrated safety technology for various industrial customers. Through the IoT communication standards such as OPC UA, POWERLINK and openSAFETY, and B&R's powerful Automation Studio software development environment, B&R constantly redefined the future of automation engineering. B&R maintains a continuous spirit of innovation and provides customers with more streamlined and exceeding-precise cutting-edge technologies and solutions in the field of industrial automation.
For more information visit: http://
Breaker Rcbo,Rcbo Protection,Leakage Protection Rcbo,Leakage Protection Switch
ZHEJIANG QIANNA ELECTRIC CO.,LTD , https://www.traner-elec.com