Automated warehouses use a large number of large storage equipment, such as high-bay shelves; handling equipment, such as pallets, forklifts, lifts; automatic transmission track and information management system, to achieve automation of the storage enterprise.
The core content of the warehousing business can be divided into five main parts: warehousing operations, warehousing management, outbound operations, financial settlement and query statements.
For the needs of third-party logistics companies, they will not simply stay on the above basic functions, they will also provide customers with various statistical information. Such as "shelf life report", "safety inventory report", "point map", goods flow frequency" and other information. But in fact, this information has been recorded in the process of warehouse management, only need to be based on each customer's special It is ok to require the corresponding production.
Warehouse management
The nature of warehousing activities 1, the productivity of warehousing activities 2, the non-productive nature of warehousing activitiesWarehouse management
The basic functions of warehousing 1. The basic economic benefits of warehousing are four aspects: storage, assembly, classification and intersection, processing (extension), etc. 2. The basic service benefits of service warehousing include on-site storage, distribution classification, combination, production. Support and five aspects of market imageWarehouse management
Conceptual elaboration Editing warehousing management is the management of materials in warehouses and warehouses. It is the planning, organization, control and coordination process of warehousing organizations to provide efficient warehousing services in order to make full use of their warehousing resources. Specifically, warehousing management includes the acquisition of warehousing resources, warehousing business management, warehousing process management, warehousing operations management, custodial management, security management, various management tasks and related operations.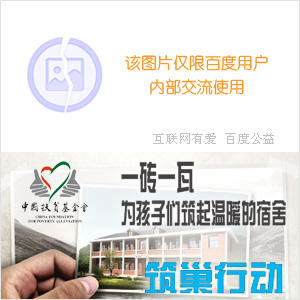
(5 photos)
Warehousing management is an economic management science, but also involves the application of technology science; it is a marginal discipline. The connotation of warehousing management changes with its expanding role in the socio-economic field. Warehouse management, that is, library management. It refers to the management of the warehouse and its inventory items, and the storage system is an indispensable subsystem in the enterprise logistics system. The overall goal of the logistics system is to provide customer-satisfying services at the lowest cost, and the warehousing system plays an important role. Warehousing activities can help companies improve customer service levels and enhance their competitiveness. Modern warehouse management has brought about fundamental changes from static management to dynamic management, and puts forward higher requirements for the basic work of warehouse management.Warehouse management
Task Editor 1. Use market economy means to obtain the largest allocation of storage resources. 2. Organize management institutions with high efficiency. 3. Carry out business activities based on the principle of continuously meeting social needs. 4. Organize warehouse production with high efficiency and low cost. 5. Establish a corporate image with quality service and credit. 6. Continuously improve the management level through institutionalized and scientific advanced means. 7. Improve the quality of employees from the technical to the spiritual level.Warehouse management
Basic Principles 1. First-in-first-out principle (FIFO). The materials that are put into the stock first are given out of the warehouse when the materials are dispensed, which reduces the quality risk of the stored materials and improves the use value of the materials. Second, the principle of locking the location. A certain material is fixed in a certain location, and the location of the physical object must be consistent with that in the ERP system. The location code is just as important as a person's home address. Without a fixed location, you can't quickly find the relevant material. Third, the special material-specific principle, do not arbitrarily use the corresponding order materials. Fourth, the ABC management principles of inventory: the amount of Class A materials may only account for 10~15% of the inventory, but the value of goods can account for 60~70% of the inventory value; the amount of Class B materials may only account for 20~35% of the inventory. However, the value of goods may account for 15~20% of the inventory value; the quantity of Class C materials may account for 50~70% of the inventory, but the value of the goods may account for 5~10% of the inventory value. Therefore, it is necessary to strictly control the key minority and minor majority, that is, to strictly control the A and B categories. 5. The principle of “six insufficiencyâ€: 1. If there is a delivery note and there is no physical object, it can not be put into the warehouse; 2. If there is a physical object without a delivery note or the original invoice, the procedure cannot be completed; 3. Incoming materials and delivery If the number, specification and model of the goods order are different, the procedures for entering the warehouse cannot be completed; 4. If the IQC inspection fails, and there is no signing approval for the use of the leader, the procedure for entering the warehouse cannot be completed; 5. If it is not used for storage, it cannot be used first. Procedures for entering the warehouse; 6. The delivery slip or the invoice is not the original one. Sixth, the "five no hair" principle: 1, no bill of materials, or the bill of materials is invalid, can not issue materials; 2, the procedures do not meet the requirements, can not issue materials; 3, unqualified materials, unless Some leaders have agreed to use it, otherwise they cannot be issued; 4. Materials with incorrect specifications and missing accessories cannot be issued; 5. Materials that have not been processed for warehousing cannot be issued. Seven, one outbound principle: material delivery must be completed accurately, in a timely manner, and the materials used in the production line must be pulled back to the location of their own production line, and can not be stacked in the warehouse to avoid confusion and errors. Eight, access control principles: 1, in addition to material management personnel and handling personnel due to work needs, other personnel without permission, will not enter the warehouse; 2, no one is allowed to carry materials privately when entering and leaving the warehouse; 3, when guests are inspected, must You can enter the warehouse when accompanied by a person above the supervisor level. IX. Principles of “Daily Days and High Daysâ€: 1. Each warehouse manager performs self-confirmation and verification of relevant accounts on the day at the end of daily work to ensure balance of accounts and identify deficiencies. Timely improvement, the next day can be improved. 2. Check the material warehouse in charge for at least 1~2 times a day to ensure the quality, safety and 6S status of the materials in the warehouse are up to standard, to ensure that the materials are correctly identified, and the returned materials should be returned to the supplier or placed in the return area. So as not to cause sluggishness. 3. The documentary of the warehouse manager on the day must be passed to the record clerk, and the documentary of the hiring officer must be entered into the system on the same day. X. The principle of trade-in: For the materials with regulations, strictly implement the principle of retiring the old and renewing the new ones.Warehouse management
Custody Principles Editor 1. Keep it facing the channel. In order to make the items convenient for entry and exit, it is easy to move in the warehouse. The basic condition is to keep the items facing the passage. 2. Store as much as possible at a high place to improve storage efficiency. Effective use of the internal volume of the library should be placed as high as possible. To prevent damage and ensure safety, storage equipment such as scaffolding should be used whenever possible. 3. The location is selected based on the outbound frequency. Items with high shipping and purchase frequency should be placed close to the entrance and exit, easy to work; items with poor fluidity should be placed far away from the entrance and exit; seasonal items should be selected according to their seasonal characteristics. 4. The same variety is kept in the same place. In order to improve work efficiency and storage efficiency, the same item or similar items should be kept in the same place. The familiarity of employees with the placement of items in the library directly affects the time of entering and leaving the warehouse. It is also efficient to place similar items in adjacent places. An important method. 5. The location to be kept according to the weight of the item. When placing the place, place the heavy items underneath and place the light items on top of the shelves. Large items that require manual handling are based on the height of the waist. This is an important principle for improving efficiency and ensuring safety. 6. Arrange the storage method according to the shape. It is also important to store the shape according to the shape of the item. For example, the product to be pushed should be placed on a tray or shelf for storage. 7. Based on the principle of first in, first out. An important part of custody is for items that are prone to deterioration, easy to break, and easy to be corrupted. For items that are prone to degradation and aging, the principle of first-in, first-out should be used as much as possible to speed up the turnover. Due to the diversification and personalization of goods, the principle of short service life is very important.Warehouse management
Main activities to edit the type of enterprise warehousing activities Enterprises can choose to build their own warehouses, lease public warehouses or use contracted warehousing to store materials and commodities to prepare storage space. 1) Own warehouse warehousing, compared with public warehousing, enterprises can use their own warehouses for warehousing activities to control warehousing to a greater extent, and management is more flexible. 2) Lease of public warehouse warehousing, companies usually lease public warehousing that provides business services for storage. 3) Contracted warehousing, contract warehousing companies can provide professional, efficient, economical and accurate distribution services. Whether a company is self-built warehouse or leased public warehouse or contracted warehouse needs to consider the following factors: total turnover; stability required; market density. General business procedures for warehousing 1) Signing a warehouse contract. 2) Acceptance of goods. 3) Handling the warehousing procedures. 4) Cargo storage. 5) Contents of goods storage and storage management 1) Ordering and delivery. 2) Inspection at the time of purchase and delivery. 3) Storage and loading and unloading operations in the warehouse. 4) Location management. 5) Stocking operations. The combination of products in storage, proper loading and distribution packaging, grouping and other activities is to improve the efficiency of loading and unloading, make full use of transportation tools, and thus reduce transportation costs. Reasonable and accurate warehousing activities will reduce the reloading and flow of goods, reduce the number of operations, and adopt mechanized and automated warehousing operations, all of which will help reduce the cost of warehousing operations. Excellent warehousing management, effective storage and maintenance of goods, and accurate quantity control, thus greatly reducing the risk of warehousing. Division of warehouse management and specific details: (electronic product processing factory warehouse) First, the receiving group (receipt group): This piece of personnel is mainly responsible for checking the number of incoming containers and checking whether the outer packaging is damaged (if found If the damaged outer packaging, immediately notify the IQA department to check whether the product inside the outer packaging is damaged. If there is any damage, immediately return the goods to the delivery company. If there is no damage, it can be stamped in the outer box by the IQA department. After the above checks are completed, the receipt of the goods is confirmed. After receiving the warehouse, the receiving group personnel must also count the small packages inside each box of goods (in the case of a relatively small number of cases). If the number of boxes is large, it is 30%. Check the amount to compare. After all the above steps have been completed, it is necessary to notify the incoming inspection department IQA in writing (send inspection). The department mentioned above will carry out the inspection. The following will explain its working steps in detail. Second, the incoming inspection department IQA: They mainly test according to a specification sheet ("Employee Work Instructions", generally referred to as SIC) of the company when the supplier is required to make this material. Whether it meets the requirements of the company. If the non-conformity will contact the supplier, request a replacement. All incoming materials will be passed to the next group, the sending group. (IQA does not belong to the warehouse, it belongs to the quality management department, it is only the needs of the program, so it is placed in this link of the warehouse, and is not within the jurisdiction of the warehouse.) 3. The sending group (storage and distribution): general electronic product processing The factory is divided into: 1. Electronic component warehouse: need to have strict temperature and humidity environment monitoring, mainly store some capacitors, resistors, BGA, IC and other series of expensive electronic materials that require high temperature and low temperature. 2. Material warehouse for assembly and packaging: mainly put some relatively bulky materials, such as the metal casing of the electronic product, screws, the thick power cord and the carton required for the outer packaging shipped to the customer. Later, if a customer places an order, then the company will calculate the materials needed for each product (according to the BOM), and each material needs several issue orders to be sent to the personnel of the issue group. Then, according to the above quantity, it is distributed to the production line for production. After the production line is finished, it is inspected by the QA group of the quality management department and then entered into the warehouse finished product warehouse. The personnel of the finished product group are received according to the documents. Fourth, the finished product group: They are mainly responsible for receiving the inventory of the number of finished products in the production line and the inventory of the number of products shipped to the customer. In short, if you want to do a good job in warehousing management, I think it should be done in the same way as accounts, goods, and cards. This means that the account represents a system software (such as SAP enterprise account management software) that manages daily inbound and outbound goods. It is all the materials and finished products in the warehouse; the card is a card filled in form for each material and finished product. Therefore, all three must be consistent, otherwise it will indicate an error. Commonly used methods to ensure the accuracy of the account card: cycle inventory. That is: before entering or sending materials, the number of cards is checked by the number of material card balances. If the next step is to send the materials, the card will be increased or decreased after the materials are sent, and the number of cards will be checked again. Prevent mistakes caused by human habitual thinking. There must also be a principle of delivery of materials and finished products on a first-in, first-out basis. This means that the materials that have been collected first must be sent to the production line. The monthly labels attached to the outer packaging of the materials can be used to identify those materials that are the earliest materials. The same is true for the finished product, and the finished product that was first put into the production line is shipped first with the shipper.Warehouse management
Note Editing 1. Whether it is possible to allocate human resources for effective operation is one of the important evaluation criteria for efficient warehouse management. Manual management techniques can help warehousing companies that are plagued by employees, assist managers in determining the number of warehousing employees needed, and can use engineering labor standards and support systems to assess the performance of warehousing workers. In addition, companies should provide incentives to teams of employees rather than individuals to maximize the team's potential. There are a number of warehouse management systems that lack consideration in terms of manual management and performance appraisal, or lack of connectivity to manual management. 2. Warehouse layout design and equipment improvement As the hub of the logistics system, whether the layout of the warehouse reasonably affects the efficiency of the entire library. For example, warehouses can be divided into different picking areas by product category. In this way, the whole box, the unpacking, and the whole plate can be separated to work, which can avoid the disorder of the site and reduce the damage of the goods. Recently, Yibo Logistics Consulting Research pointed out that the equipment improvement for warehouses can also be reflected in the packaging of goods and materials. Advanced packaging not only provides effective protection for goods, attracts cargo owners (especially those that are difficult to store), but also facilitates the mechanization of storage. On the other hand, the automatic transmission and reception of modern warehousing information requires not only uniform size and specifications of materials packaging, but also requires that material information be reflected on the packaging through barcode and other technologies, which is precisely the goal that material packaging standardization should achieve. Therefore, improving the packaging of materials is conducive to the automation of warehouse management. 3. The function of carrying out additional value-added service warehousing is not limited to pure storage function nowadays. Therefore, providing additional value-added services, such as circulation processing, combination packaging, labeling, etc., can realize additional value-added functions of the warehouse, improve revenue and improve Customer Satisfaction 4. The central command center of the central command center in the warehouse can be a project management agency that guides the completion of the new inventory, the results of the report, and the progress of each department, while maintaining contact with external customers. The command center should consist of two parts: the person and the system. In addition to the system functions of “inside the wall†including inbound and outbound management, inventory management, order management, picking, review, basic information management of goods and goods, replenishment strategy, and intra-bank mobile combination, Also consider the connection between the warehouse management system and the transportation management system, customer management, and employee management systems. The role of people in the command center cannot be replaced by technology. The logistics project leader needs to optimally allocate limited resources based on a large amount of data. Warehousing is not an automated business. There are too many uncertainties in warehousing. It is necessary to assume the role of general manager in charge of the inside and outside of the warehouse.Warehouse management
Warehousing and logistics service editing Logistics warehousing and distribution service has become the core industry link of China's e-commerce. Providing a comprehensive and complete logistics warehousing and distribution solution has become a problem that many small and medium-sized sellers and e-commerce suppliers must pay attention to. The logistics warehousing and distribution network system independently developed by Shanghai Zhichang Warehouse Logistics Distribution Supply Chain Service Provider has become the new darling of e-commerce. It can not only bind, Taobao, Jingdong, No. 1 shop and other e-commerce back-end logistics platforms to help enterprises. The seller directly orders the goods in the background, and more importantly, can provide different warehousing logistics distribution solutions for different enterprise sellers. Zhi factory can provide low-cost logistics distribution mode, and can also provide the fastest logistics distribution solution. As a small number of warehousing logistics and distribution enterprises that can handle 100,000 orders per day, it has become a long-term cooperation partner of many brands such as Sanlianliang, Converse and Shanghai Rihua.Warehouse management
The 8 key management mode editing management can be simply summarized as the key management mode of the 8 songs: the first song: chase. Warehouse management should have the ability to trace information, and extend to the logistics and transportation and supplier production and delivery status, and the supplier's production allocation and actual shipment status. At the same time, warehousing management must conduct ETD/ETA connection traceability with logistics providers: ETD (Estimated to Departure) - How much is the number of terminals leaving the supplier's factory and the number of terminals leaving the supplier's outsourced warehouse? How much does the logistics and fourth-party logistics vehicles leave the departure? ETA (Estimated to Arrival) - How much does the third-party logistics and fourth-party logistics vehicles arrive at the destination? How many terminals arrive at the company's factory? Arrived at the company's production line How much is the warehouse? The replenishment status is connected to the VMI Min/Max inventory system. The second song: Receive. The warehouse should use barcode or more advanced RFID scanning to confirm the feeding status when receiving the goods. The key points include: when the supplier delivers the goods, the delivery information does not purchase the VPO number, and the warehouse should promptly find the relevant department to find out the reason and confirm Whether the goods should be replenished at this time; if there is a number of boxes that do not reach the minimum packing quantity when the materials are inventoried, they should be carefully unpacked and unrecognized before they can be received; when the goods receipt scan is confirmed, such as If the system does not accept the order, the relevant department should be promptly found to find out the reason and confirm whether the goods are included. The third song: check. The warehouse should have the ability to inspect the goods. For Class A materials (only a few suppliers can choose from a limited competitive market and a Class A material for the exclusive supply market of monopoly sources), special control, strict quantity, independent warehouse, 24-hour security Monitoring; establish a package material consumables exemption system, requiring suppliers to unconditionally replenish and replace the defective materials at the line side; analyze the material storage time limit and set the time limit for processing the bad materials. The fourth song: Chu. Material into the warehouse can not be grounded or at least done (stored on the pallet, can be moved at any time), each material can only have one number of boxes or a few boxes concentrated on one pallet, temporary storage time automatically Warning, try to achieve Bin-Location control, do No Pick List, can not move! The fifth song: pick. The picking is done according to the order of the work order consumption. It can be used to pick up the material according to the light number indication (also known as Pick to Light). It is best to automatically scan to the debit action when picking the material, and timely change the inventory information to inform the central Schedule replenishment. The sixth song: hair. The warehouse issuance according to the work order, the order, the work order, the preparation order and the picking list should be three-in-one, so that the on-site work order can be used at a glance, and the automatic scanning system is used together with the information transfer operation. The seventh song: disk. The finishing of the disc is always followed by the principle of scattered bulk. For example, the total number of 1 materials is 103, which is 10 boxes (10 per box) plus 3 zeros. The method of counting the counts on the inventory sheet should be written as 10 boxes × 10 + 3 = 103. For materials to be classified, to determine the inventory time of various materials, periodic inventory can be divided into daily / weekly / monthly; daily inventory with Move List inventory; monthly checkout at 12:00 noon The goal to be completed is set. The eighth song: Retreat. The whole package is returned to the processing principle, the processing time limit and the number of treatments should be able to achieve the whole package or retreat or the entire batch of light retreat at 3 pm every Friday, so that the Force Parts system replaces the RMA ( Return Material Authorization), in conjunction with the VMI Hub Return Staging Area, requires suppliers to make free shipping packages.Warehouse management
A warehouse is a general term for buildings and places where items are stored and stored. The warehouse function in logistics has evolved from simple material storage and storage to the functions of receiving, sorting, measuring, packaging, sorting, distributing and saving of materials. Library management refers to the management of commodity storage space. The problems that should be paid attention to in warehouse management operations are: 1. The inventory goods should be managed by positioning, and the meaning is similar to the design of the commodity allocation chart. The principle of different product classification and division management is stored and placed on the shelf. The warehouse must be divided into at least three areas: first, a large number of storage areas, that is, stored in a full container or pallet; second, a small storage area, where the zero-demolition items are placed on the display rack; third, the return area, Place the items that are about to be returned on a dedicated shelf. 2. After the location is determined, a configuration map should be made and posted at the entrance of the warehouse for easy access. The small storage area should be as fixed as possible, and the whole storage area can be used flexibly. If the storage space is too small or is a frozen (storage) library, it can be used flexibly without fixing the position. 3. Store items that are not in direct contact with the ground. One is to avoid moisture; the second is due to the provisions of the fresh-keeping instruments; the third is to pile up neatly. 4. Pay attention to the temperature and humidity of the storage area, keep it well ventilated, dry and not wet. 5. Waterproof, fireproof, anti-theft and other facilities should be installed in the warehouse to ensure the safety of the goods. 6. The stock storage shelf should be set up with an inventory card. Color management methods, such as weekly or monthly labels of different colors, can also be used to clearly identify the date of purchase. 7. The warehouse management personnel should communicate with the ordering personnel in time to facilitate the storage of the goods. In addition, early warning notices of insufficient stocks should be filed in due course to prevent out of stock. 8. In principle, warehouse storage and pick-up should be carried out as needed, as needed, but in view of efficiency and safety, it is necessary to formulate operating hours. 9. The goods must be registered in order to clear the responsibility. However, some commodities (such as frozen and refrigerated goods) are time-sensitive, and the combination of store inventory and warehouse inventory is also adopted. 10. The warehouse should pay attention to the access control management, and should not enter it casually.Warehouse management
Warehousing Management System Editing Warehousing Management System Warehousing Management is also an important part of modern logistics management. Warehousing management is important for ensuring timely supply of the market, reasonable reserves, accelerating turnover, saving materials, reducing costs and improving the economic efficiency of enterprises. Therefore, the warehouse management system has become an important part of the modern company management system. It mainly includes the following aspects: 1. The company's warehouse planning management system 2. The inventory management work rules 3. The company's material storage and storage regulations 4. The company's storage management measures V. Company Material Numbering Method VI. Warehouse Management Measures VII. Company Product Requisition Details VIII. Company Delivery Management Regulations IX. Return Management Regulations 10. Purchase Management Regulations 11. Regulations for Transfer Management 12. Provisions for Outbound Management III. Regulations on the management of goods in and out of the warehouse 14. Regulations on product storage of the company 15. Storage safety management methods Advertising management system The role of advertising is not only to promote the company's visibility and reputation, but also to shape the image management system of the enterprise. An important content of marketing management of the company is the basis of corporate marketing activities is an important means to ensure that the company achieves sales targets. The advertising management system of modern enterprises mainly includes an advertising and publicity management system. Four companies on the new product promotion regulations five principles of advertising planning six advertising plan preparation points seven marketing and advertising plan preparation guide eight companies to create their own advertising operation process nine television advertising film operation process ten television advertising film production process eleven storefront Advertising production rulesWarehouse management
Warehousing Management Mode Editing VMI: In terms of raw materials, valuable and self-made suppliers are stationed in VMI Hub. The production stage is as non-stock as possible (stock is supplier), and suppliers do line-side warehouse services. In terms of finished product picking, the finished goods inventory is stored at the shipping port, arranged by the same packing number and SKU number, and the packaged order goods are placed on the pallet at the time of shipment. There are two shipping instruction forms on the document, the Delivery Note and the Transportation Order. It is best not to exceed 4-8 hours from picking the material to leaving the product. VMSA: The Hub located at the customer's office, according to the customer's sales situation and the variables of the Forecast, negotiate with the customer to adjust the Mini/Max of the Hub, and automatically respond to the inventory and replenishment volume to the manufacturing base when the customer picks up the goods. Pick To Light (according to the light number indication during production): Picking according to the production work order, because the CTO orders are more samples, the picking is more frequent; because the models are different but close, so the picking area should be set N Area, separate the different picks of each model and mark them. Pick To Light's light control is extremely relevant to the work order barcode information. Merge: In the CTO mode, the high-end components of the final product required by the end user are Bounded (tied together) in transit, and shipped together to the designated place for delivery, which is Merge. Usually Merge is entrusted to the logistics industry to do, the fourth party logistics can do the Merge function, the next step is to test the assembly and collection business functions at the final customer desk.Warehouse management
Warehousing management steps edit the first step: check. The picking is done according to the order of the work order consumption. It can be done by the light number indication (also known as Pick to Light). It is best to automatically scan to the debit action when picking the material, and change the inventory information notification center in time. Schedule replenishment. The second step: picking. The third step: chase. The fourth step: send. The warehouse issuance according to the work order, the order, the work order, the preparation order and the picking list should be three-in-one, so that the on-site work order can be used at a glance, and the automatic scanning system is used together with the information transfer operation. The warehouse should have the ability to inspect the goods, and special control for Class A rogues (only a few suppliers can choose the limited competitive market and exclusive supply of Class A materials for monopoly sources), strictly control the number, independent warehouse, 24-hour security Monitoring; establish a package-free consumables-free inspection system, requiring suppliers to replenish and replace the defective materials at the line side without any preconditions; analyze the material storage time limit and set the time limit for processing the bad materials. The fifth step: save. The sixth step: the disk. For example, the total number of 1 materials is 103, which is 10 boxes (10 per box) plus 3 zeros. The method of counting the counts on the inventory sheet should be written as 10 boxes × 10 + 3 = 103. Packing up and rectifying the discs always follows the principle of scattered bulk. For materials to be classified, so as to determine the inventory time of various materials, the inventory can be divided into daily/week/monthly on-time inventory; the daily inventory is matched with Move List; the checkout is performed at 12 noon on the 1st of every month. The goal to be completed is set. At the same time, warehousing and management must carry out ETD/ETA connection traceability with logistics providers: ETD (Estimated to Departure) - how much is the number of terminals leaving the supplier's factory and the number of terminals leaving the supplier's outsourced warehouse? How much does the logistics and fourth-party logistics vehicles leave the departure? ETA (Estimated to Arrival) - How much does the third-party logistics and fourth-party logistics vehicles arrive at the destination? How many terminals arrive at the company's factory? Arrival at the company's production line How much is the side warehouse? The replenishment status is connected to the VMI Min/Max inventory system. The warehouse should use bar code or improve the RFID scan of the predecessor to confirm the feeding status. The pivot point includes: when the supplier delivers the goods, the delivery information does not purchase the VPO number, and the warehouse should find relevant parts in time to find out the reasons. Confirm whether the goods should be collected at this time; if there are materials in the inventory that do not reach the minimum packing amount, they should be carefully unpacked and unfairly accepted before receipt; when the receipt scan is confirmed, If the system does not accept the request, you should find the relevant part in time to find out the reason and confirm whether the goods are included. Step 7: Check. Step 8: Retreat. Return to the principle of returning the whole packageWarehouse management
How to do a good job in warehousing management Editing warehousing management is an important part of enterprise management. It is a necessary condition to ensure the smooth progress of the production process of enterprises, and an important way to improve the economic benefits of enterprises. "Boss" magazine said that according to the position and role of warehousing management in business management, warehousing management should be done from the following aspects. 1. Establishing a sound warehouse quality assurance system Warehouse quality management is the specific application of the theory and method of “total quality management†in the technical and economic activities of warehouses, and is the necessary way to improve the economic effects of enterprises. Total quality management advocates to extend the management's reach into all aspects of the operation. It is not the case. Through the methods provided by the company, the company managers can find the weak links that affect the warehouse, so as to take improvement measures, which will reduce the supply cost and improve the enterprise. Economic benefits are of great significance. In the process of running the quality assurance system, all managers must firmly establish the idea of ​​“quality first†and work proactively to meet the requirements of good supply, low consumption and high efficiency. 2. Strengthening the basic management of warehousing management Although the warehousing activities serve the production, but different from the production activities, they have their unique labor objects and methods. In the process of warehousing activities, some basic links such as material inspection, warehousing and warehousing are the main contents of warehousing business activities. The quality of these basic links is directly related to whether the warehousing work can proceed smoothly and directly affect the entire warehousing. The quality of work is good or bad. Therefore, enterprise managers should strengthen the management of each basic link, which is the prerequisite for doing a good job in warehousing. 3. Material storage and maintenance is the central content of warehousing management. After a rigorous inspection at the time of storage and acceptance, it enters the storage stage. Therefore, after the materials are put into storage, the “fourth positioning†and “five-five positioning†must be implemented. "The logo is clear and reasonably stacked. The enterprise managers must do the work of "three transformations", "five preventions", "5S", etc. The above work is the necessary measures to keep the materials from being lost during storage, but because of the physical capital The nature, the influence of natural conditions or the cause of man-made causes the loss of the quantity of materials. In this management mode, material loss can be avoided, and it is difficult to completely avoid it. Generally, it is difficult to completely avoid it called natural loss. Therefore, it is required that the storage staff need to be able to grasp and use the nature of the stored goods and the quality change law that is affected by various natural factors. The enterprise manager fundamentally adopts the principle of “prevention first, prevention and control combinationâ€. Early prevention and early treatment, to minimize and reduce the loss of goods.Pharmaceuticals,2-Methyl- Propanoic Acid Monohydrate Price,2-Methyl- Propanoic Acid Monohydrate Free Sample,Pure 2-Methyl- Propanoic Acid Monohydrate
Zhejiang Wild Wind Pharmaceutical Co., Ltd. , https://www.wild-windchem.com